Replacing sailboat tanks that live in the bilge, under the cabin sole, is a very big job. Here I detail how I researched the job and chose the best boat yard to perform the work.
I did not want to buy a project boat. Unfortunately, my search for a suitable blue water boat left me with few options. So when it came down to brass tacks I was willing to take on a project boat if I could get it for a good price; a price where the previous owner essentially shared some of the cost of having the refit done professionally.
Even before the survey I knew that S/V Counterpoint was such a boat. From poking around in the bilges Francis (my broker) and I were able to see a few things things that looked like big projects:
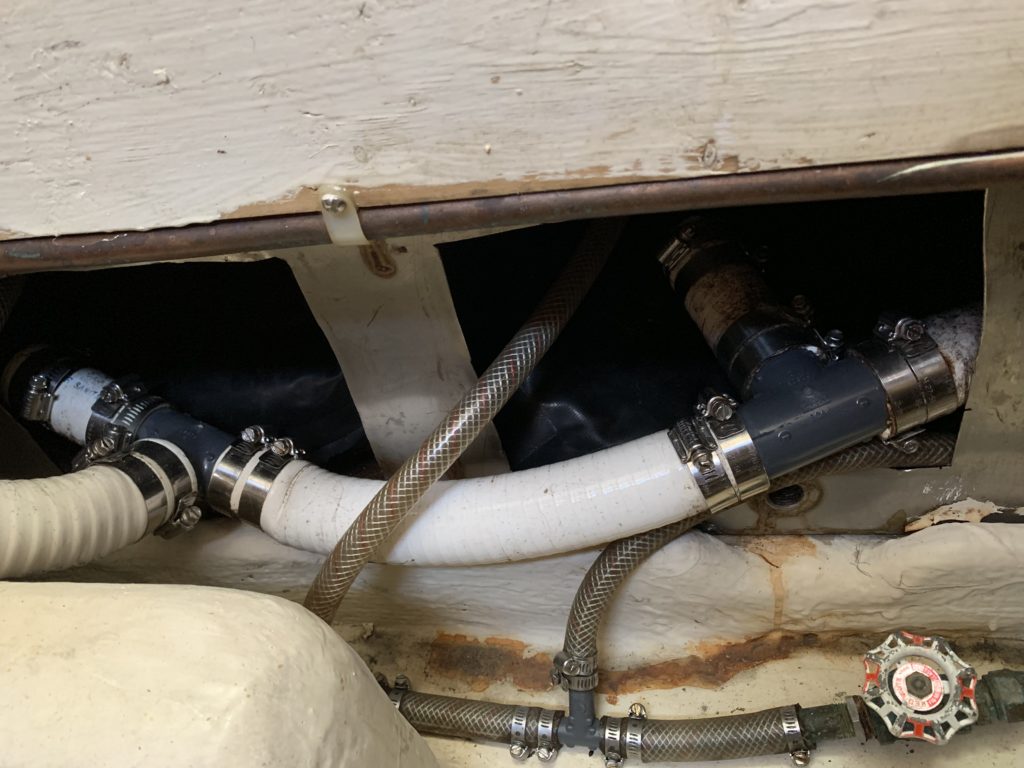
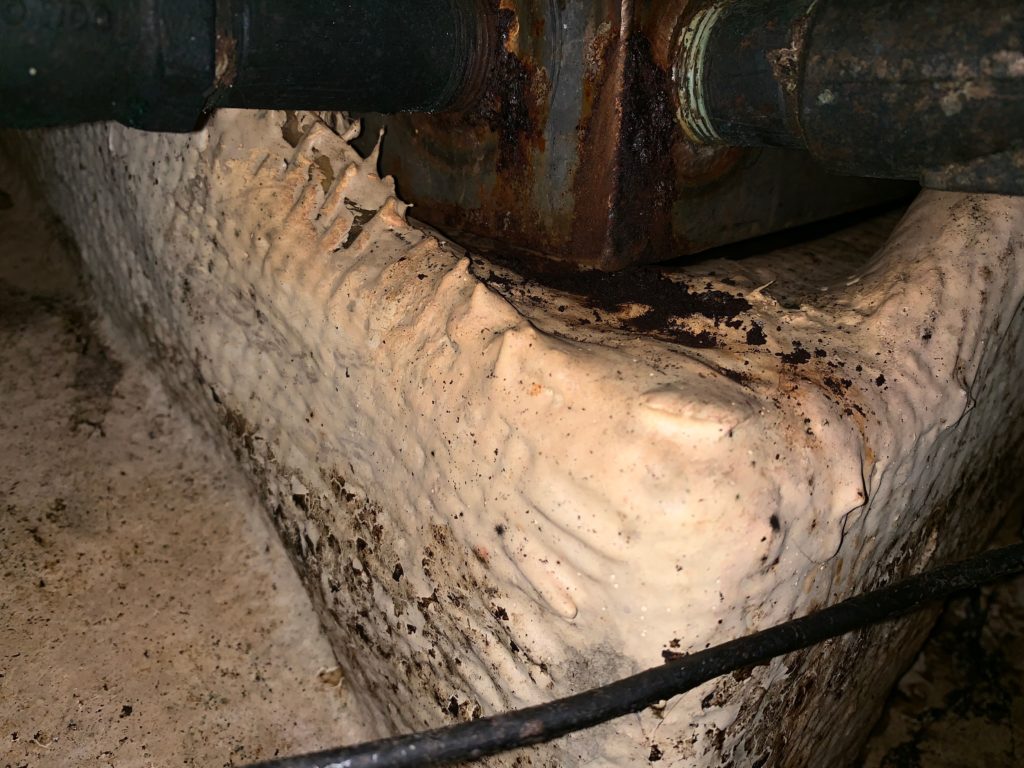
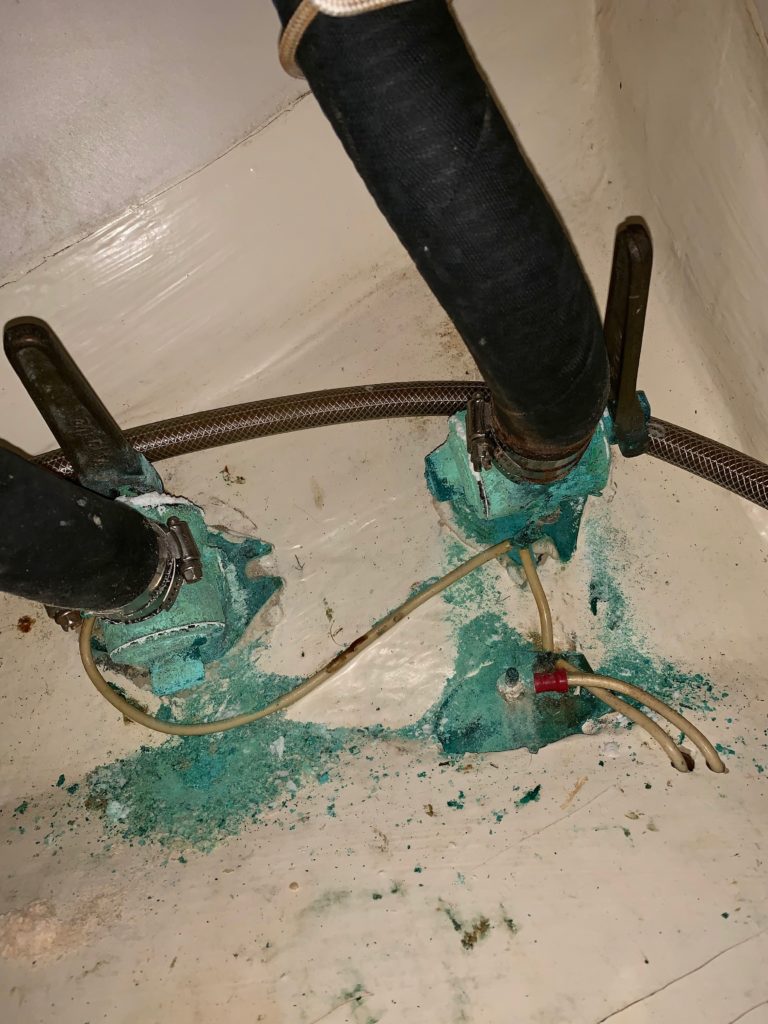
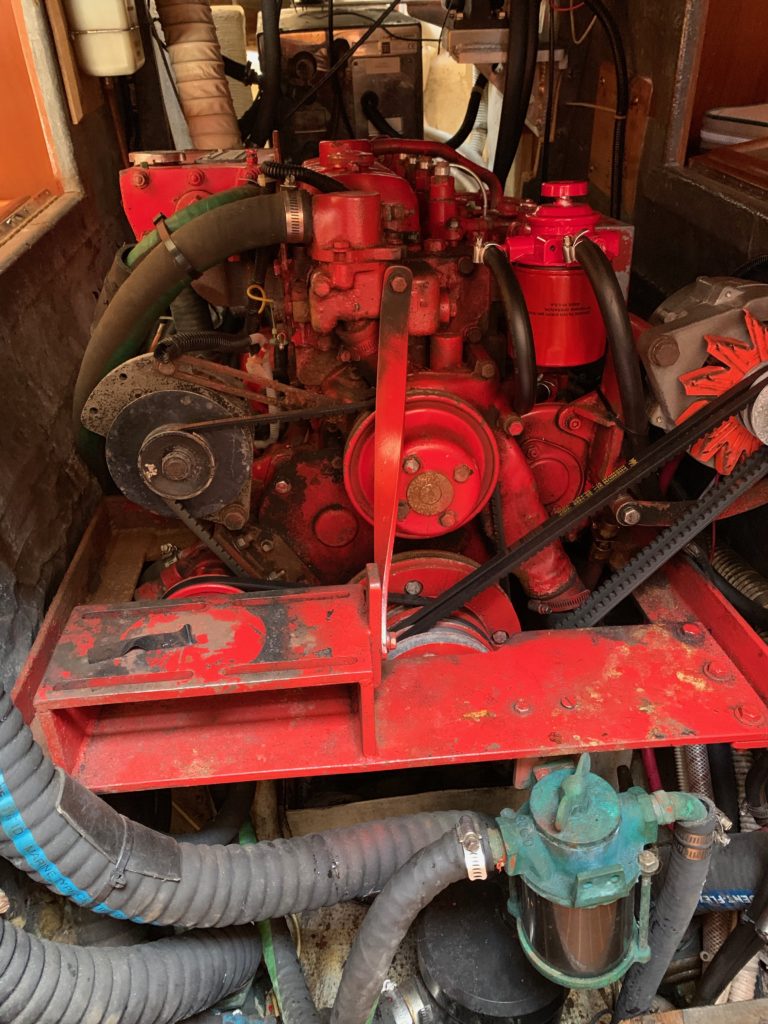
Before I would make an offer I scoured the internet for information about these projects and started calling boat yards that I heard anything good about to get estimates for these projects.
This information would strongly inform my decision whether or not to make an offer and how much I should offer.
The Problems in the Bilge
The internet yielded critical information relatively quickly: the tank replacement would be far and away the most expensive potential refit project.
The reason for the expense was the difficulty in accessing the tanks. When S/V Counterpoint was built three fuel tanks and the two water tanks were placed on the hull of the boat. Then the cabin sole was built on top of the tanks. Then the interior was built on top of the cabin sole.
So replacing water and fuel tanks in the bilges could require removing a significant portion of the boat’s interior. Disassembling, reassembling and potentially replacing parts of this interior would be a very labor intensive process.
Further complicating matters: the tanks might have to be constructed inside Counterpoint’s cabin if they would be too big to fit through the companionway.
Getting Quotes from Marine Vendors
Once I knew the potential scope of the tank replacement project I knew I’d be spending $50,000-$100,000 on Counterpoint’s refit. Naively I thought that shopping around a potential 6 figure project would mean that boat yards and other vendors would be eager to work with me.
That was NOT the case. Instead I spent 6 months chasing yards around to figure out which yard to choose for the project:
- At least 2 yards simply never returned my calls or emails (There may have been a third, this was so frustrating I didn’t keep good records)
- A half an hour into a call with one yard, when I mentioned I was getting other quotes for the work said “we don’t estimate jobs competitively” and ended the call the same minute
- After several calls with a yard, who was aware that I was getting other quotes, scheduled a date and time to come aboard Counterpoint to put together a detailed estimate. They did not show and did not call. I was never able to get a hold of anyone other than a receptionist at that yard again.
- Ultimately, 3 yards got people aboard Counterpoint and put together detailed estimates for the tank replacement projects
Only about 1/3 of the boat yards reached out were willing to put together a quote for all this work. It was shocking and frustrating. Now I know and perhaps if it happens to you it will be less of a shock.
I was shocked at how many boat yards didn’t seem to want money.
Request For Quote (RFQ) Template
After the first time I was ghosted by a boat yard I realized finding the right yard for the job was going to be a numbers game. After I took ownership of Counterpoint I put together a package that I could send to yards with the details of the project. After I spoke to someone at the yard about the work I would follow up something like this email:
I was told that emailing you is the best way to get an estimate for this work on my Bristol 45.5. I have attached a document with details of the work that I’m looking to have done over the winter. Please email me or call me at … if you have any questions.
I look forward to hearing from you,
And attach this document:
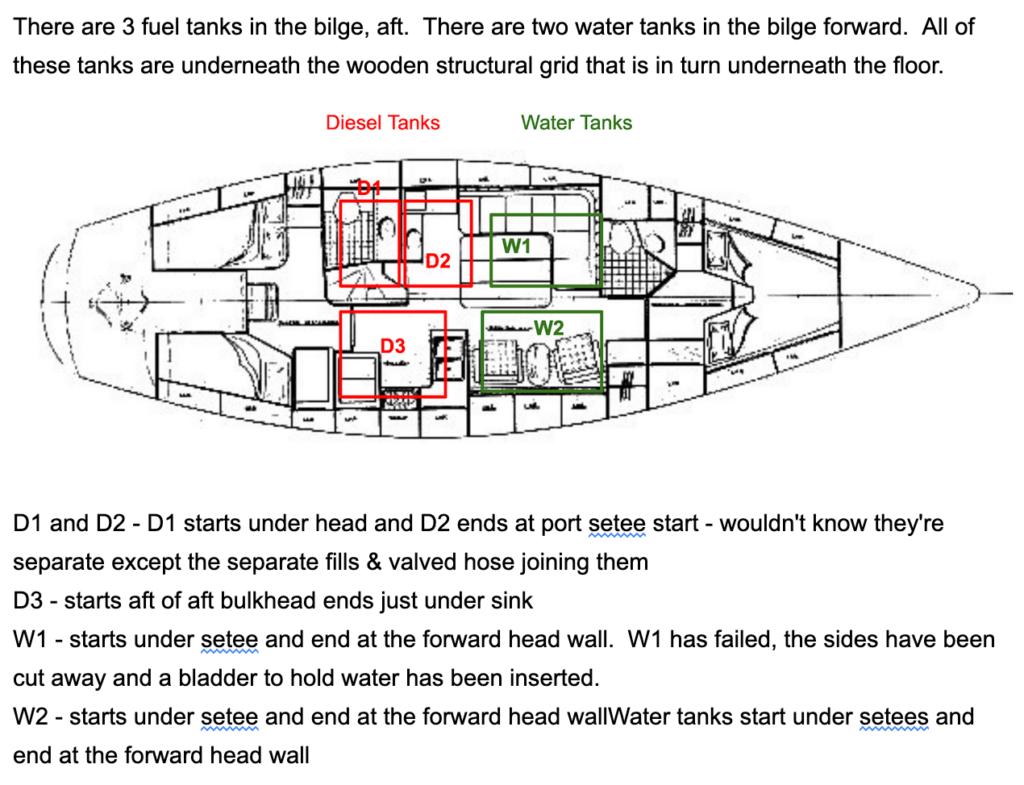
I could have put the whole RFQ into an email so it seemed like I wrote it for each yard but I thought the PDF document made it clear that I was getting multiple quotes. Presented with that email follow up the yard would either ghost me or reach out to try to figure out how to get aboard Counterpoint.
Prepare Questions for The Yard’s Visit
Before I completed the purchase of S/V Counterpoint I got two rough estimates from yards who had done similar work on similar boats. But for the final detailed estimates I would have been hesitant to trust a yard that didn’t spend some time aboard Counterpoint figuring out the project.
Fortunately, each yard willing to put together a detailed estimate was on the same page and made appointments to get aboard.
While they yard’s workers could have gone aboard to look over S/V Counterpoint without me present I made sure I was aboard when they were. I prepared a list of questions to ask and was ready to take notes on their answers and also other information they offered about the work.
The estimating party from most yards was two or three experienced workers which was a bit overwhelming; the information was coming at me fast and I was taking notes furiously. But I did my best and got many questions answered.
This part of the estimate process was very informative and I believe the most important piece of choosing the right yard for the job.
Not only did I get a real sense of how much experience the builders who would be overseeing the project had but I also took any interesting point about the boat that they noted and added it to my master list of questions. I looked at each detailed estimate through the lens of my master question list that the combined 8 workers from 3 yards raised. If the answers weren’t in the detailed estimate I followed up with emails and phone calls until I understood how each yard intended to address all concerns.
This was a very time consuming process but when I was done I was very confident with my choice of yard for S/V Counterpoint’s rebuild.
Comparing Approaches and Estimates for Replacing the Tanks in the Bilge
Taking the interior apart and putting it back together was, as expected, the most expensive part of each estimate. The quotes from the three yards differed in how much of the interior they though would need to be removed to complete the project:
- All 3 yards, Yard B, Yard N and Yard J, estimated based on removing the port and starboard setee and the cabin sole underneath the setees
- Yard N estimated based on removing the setees and the nav station (and cabin sole underneath the nav station)
- Yard J and Yard B estimated based on removing the nav station and galley forward of the refrigerator (and cabin sole underneath) to complete the project
The other major differentiator between the estimates was how much of the cabin sole could be re-used vs have to be replaced entirely.
- Yard B and Yard N estimated based on replacing some to most of the cabin sole removed to get access to the tanks
- Yard J estimated based on re-using a majority of the cabin sole they removed
Yard N and Yard J quotes, after being revised to be based on the same tank materials and the master list of concerns I curated ended up being very similar. The hours of labor were within 10%. If I removed the cost of the additional lumber for the cabin sole from Yard N’s quote the estimates for the materials required was also within 10%.
Yard B estimated almost twice as many hours and they estimated 50% higher material cost. I talked to them more and they were willing to work with me on further refining the estimate but I never got that far.
Tank Materials
Each yard recommended plastic for the water tank replacements.
The Diesel tanks were split. Yard N said they would need to be stainless steel. Yard B strongly suggested that the diesel tanks would need to be fiberglass if they were going to be the same size. Yard J quoted me both fiberglass and stainless steel diesel tanks.
As I was replacing water and fuel tanks made of stainless steel I wanted to do better. The running joke was that stainless steel “stained less”, lasting almost 40 years, but no metal tanks were completely rust free.
Ultimately I chose fiberglass fuel tanks and plastic water tanks; I was finally swayed by the arguments in favor of fiberglass fuel tanks in Nigel Calder’s Boatowners Mechanical and Electrical Manual (affiliate link).
Geographical Arbitrage
The reason I broke the estimates down to compare them in terms of labor hours instead of simply labor costs is because the yards were far enough apart that their hourly labor rates were quite different. Yard J, located well into Maine, had labor rates ranging from $55-65/hour (2019 rates not the current rates) while coming from southern New England I had become accustomed to receiving quotes with labor rates in the $100-125/hour range.
My willingness to relocate S/V Counterpoint to have this work done meant that I could potentially halve the cost of labor on the tank project; the majority of the tank project cost being labor it could (and did) make a lot of sense.
The downside of moving the boat was that my drive to check up on the boat and the work went from a little more than an hour each way to over three hours each way. Plus I had to deal with the expenses of moving the boat.
Still, in balance, it would be well worth moving the boat if I could find the right yard.
Choosing the Best Yard for the Job
After the estimate the last thing I did to finalize my decision was to check references. I spoke to the sailors who recommended the yards originally and got contact information for anyone else they knew who had work done at that yard. I also asked the yards for references; specifically other owners who had fuel and water tanks replaced.
I don’t intend to burn bridges with SavvySalt.com; perhaps even the yards that I suspect ghosted me just lost track or something. Which means I’ve shared as much about the yards I didn’t choose as I’m going to.
Yard J, Johanson Boatworks in Rockland ME, was the yard I chose. After all the research I had done I was pleased that it turned out to be an easy choice. Johanson’s estimation team and the supervisors I spoke with on the phone made the best impressions. Their estimate was by far the most detailed. Their estimate was competitive. Johanson’s references were great: they pointed me to another Bristol 45.5 owner that they had done work for and a second Bristol owner who had them replace his fuel tanks. Through another sailing contact I was able to find an owner in my sailing network who had a big refit done at Johanson. All three references were very positive.
Fuel and Water Tank Replacement Project Outcome
Like any boat project there were some complications. Fortunately there were also some parts of the project that proved less laborious than estimated.
Above I mentioned Johanson had estimated based on removing the port and starboard setees, the gally up to the refrigerator and the nav station along with the cabin sole beneath each of these. Fortunately they only needed to remove the setee and the galley sink island on the starbord side. On port they were able to get by without removing the nav station only removing the setee.
Even more impressively Johanson only made one cut in the cabin sole; they were able to lift the one giant piece of flooring out of the way without cutting it into smaller pieces and taking it out of the boat. They did all the rest of the work with a big hunk of cabin sole dangling from the cabintop!
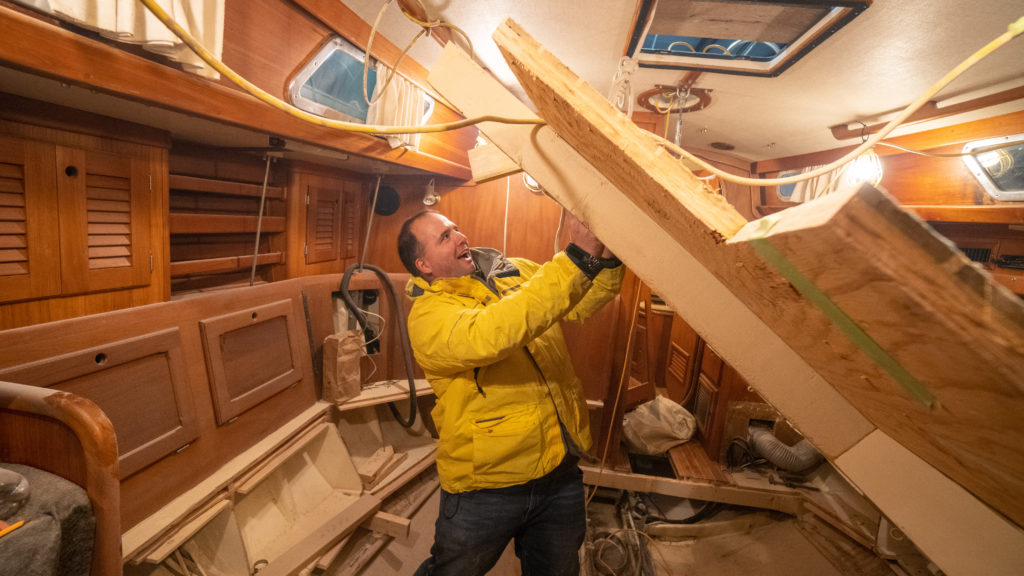
When you step aboard S/V Counterpoint you can’t tell that the interior was removed and re-installed unless you really know what you’re looking for. The level of finish seems like magic to me. They re-used all of the cabin sole which was another reason I went with Johanson; I figured the finished boat would look better that way and I’m quite happy with the result.
Some other notes about what went better than estimated and what was more difficult:
- The fuel fill and water fill lines and deck fittings needed to be replaced
- Re-building the fuel supply system was easier than anticipated
- Most of the fresh water lines in the boat were able to be preserved
- The fuel was bad enough we needed to dispose of it instead of polishing it
- The fuel disposal was able to be done very cost effectively
- Only a tiny bit of rot was found and replaced under the sole; this rot was exactly where the leaking water tank (the one with hollowed out with the bladder) would have kept the bilge wet
- We had to switch to a different tank maker who cost a bit more but was not backed up with work to keep to schedule
- The tank work was able to be done around the centerboard cable conduits so they didn’t need to be cut and re-glassed
Lastly a month or two into the sailing season I noticed there was a small hole in the top of the water tank. I swear Max, Counterpoint’s project supervisor at Johanson, was more upset when he found out about the leak than I was.
Johanson fixed the water leak aboard Counterpoint, even though she was hundreds of miles away in Rhode Island, AT NO COST TO ME.
Johanson is a different kind of boat yard. I enthusiastically recommend Johanson Boatworks in Rockland, ME. If you do work with them I’d be happy to hear about your experience as well; I expect I’ll be taking S/V Counterpoint back there for additional work in the future.
Estimate vs. Invoice
In an upcoming article about my blue water boat’s 40 year refit I compare the costs with their estimates as well as breaking down the cost by project and more.
But the one sentence summary is that the project wound up costing more than the estimate by 13% which I was satisfied with but Johanson was not. Again, simply a different kind of yard.
I hope this article helps sailors who are looking into having the tanks in their bilges replaced. I would have really appreciated reading an article like this during the spring and summer of 2019. If you’re considering or undertaking a tank replacement project I’d be more than happy to chat with you about it further in the comments below or privately if you prefer.
S/V Counterpoint Article Series
If you care to read more about my journey buying Counterpoint checkout the additional articles below:
- How I chose my Bluewater Sailboat
- Bluewater Sailboat Purchase Process
- Fuel Tank and Water Tank Replacement Project (this article)
- My Bristol 45.5’s 40 Year Refit
- 45’ Blue Water Boat Cost of Ownership
- S/V Counterpoint: Bluewater Sailboat Video Tour
Want to do the same to our 1980 Bristol 45.5 aft cockpit. We are in Mystic, Ct.
I still recommend Johanson boat works in Maine for the job: https://jboatworks.com/ – but definitely ask around and get estimates of your own.
I know every boat and every job is different, but can I ask ballpark what the price was for the water tanks
I go in to a lot of detail in this post: https://savvysalt.com/blog/my-bluewater-sailboats-40-year-refit/